OEM Cable Connectors
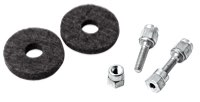
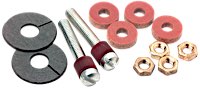
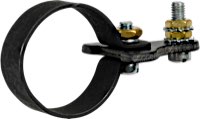
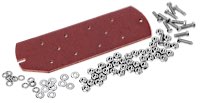
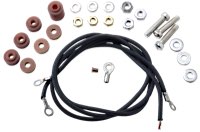
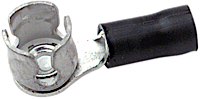
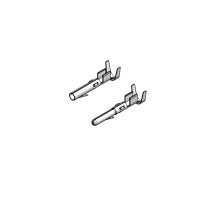
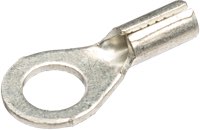
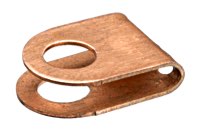
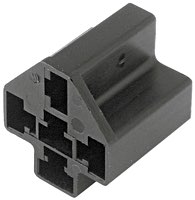
Connecting wires
Until the late 1970s, Harley-Davidson motorcycles had mainly screwed wire connections with ring lugs soldered or crimped on. This was convenient and nicely uniform. You only needed a screwdriver to loosen a connection. And the connections were vibration-proof, provided the screws were properly tightened and fitted with lock washers. This is still the case today with battery terminals.
The disadvantage
of this way of connecting wires is also obvious: each connection must be loosened individually and at the distribution points (called "terminals") there were sometimes up to four ring lugs on one screw. It wasn´t possible e.g. to just disconnect a plug from the rear fender and to disconnect the taillight wires took almost as long as removing the fender itself.
The solution was crimp connectors and connector housings, which were introduced in the 1960s in automobiles. You probably know these wide flat plugs and the sleeves for them. These were the first somewhat clunky parts. Significantly, they were called Fast-Ons". You could also organize them in connector housings to several next to each other.
With Harleys
they never existed, though. Harley-Davidson relied on round connectors and sleeves. The 2 mm thin connectors fit into housings half the size of the flat connectors and were easy to install on the motorcycle.
The next stage in the development of OEM wire connectors was waterproof and came from a manufacturer called Deutsch. With the vehicle network known as HDLan came thinner wires and the waterproof connector dwarfs from JAE. They come from the aircraft industry (JAE = Japan Aviation Electronics) and a 4-pin connector measures only 14 x 9 mm in cross section and the wires are not much thicker than 1 mm. Now all too filigree for some mechanics…
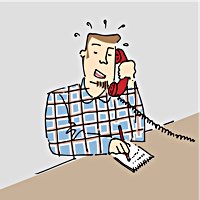
Have any questions?
Our service team will be glad to help out: Mondays - Thursdays 08:00-17:00 CET, Fridays 08:00-16:00 CET, Phone: +49 / 931 250 61 16, eMail: service@wwag.com